Nightblood 3D Print File
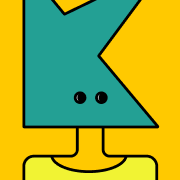
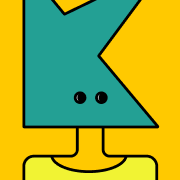
Thank you for your interest in our project! Here you can directly download the 3D files for the project, and then follow our guide below for prepping and printing the files, or you can skip a few steps and purchase the prepped print files. Below you will find a bit of background on the modeling process along with the guide on how to reproduce the same product we created.
3D Modeling
The model for the sword didn’t exist anywhere online in a form I liked, so I found reference online from the artists who had made canonized artwork for the series, and I created my own. We also wanted it to be the correct dimensions based on what the “reported” canon size of the blade was based on its listing in coppermind.
The cover of the leatherbound version of Warbreaker, which includes a 2D version of Nightblood
The initial reference and my main reference was the front cover of the leatherbound version of Warbreaker. This has the 2D vector version of the sword, which allowed me to get some really good scale and dimension reference, but it required me to interpret some 3D shapes from the 2D shapes that weren't directly apparent. Like the arrow on the cross guard.
3D Printing
The prints have all been split up to easily fit on a Prusa Mk3s sized printer. Multiple parts can be printed onto a single build plate if desired. However, it is usually a better idea to do them one at a time if possible in case one fails you only lose a single part.
I printed them in PETG with a Prusa Mk3s and a 0.6mm nozzle at layer heights of 0.3mm. It should print in different materials just fine, as well as a smaller (or larger) nozzle and different layer heights. My only possible concern with larger heights would be how well the thread in the center prints and how well it's tolerances remain so it can thread onto the metal rod well. Going with smaller layers would likely make it easier to thread.
The only part that really needs supports is the full cross guards; the rest should print fine without them, depending on your printer and layer heights. The grip pieces may need them if your printer doesn't handle overhangs well, or if you use much larger layers. Same with the thread in the center of each part, however I would try really hard to not need supports for the thread, as that would be a huge pain to remove. If you are printing at reasonable heights with a solid printer and your slicer recommends a few random supports on the thread you should be able to remove them from the slicer and print without them. For the cross guard I found that the organic supports in prusaslicer worked really well.
Assembling
Each of these files has a thread designed into the center in order to thread in a 3/8in.-16 metal rod. (3/8in. diameter, 16 threads per inch, or coarse) These rods can be found at most big box stores. You will need a rod that is roughly 60 inches (150cm) long. I would recommend going longer than that and cutting it down to size, leave a small amount of extra space at each end so the rod fits.
Before threading the rods, if you plan on sanding the plastic I would do that now before assembly. It is easier to handle the smaller parts for more heavy duty sanding to the plastic at this stage. You can also apply a first layer of bondo (I'd recommend the spot putty) or another filler and do some additional sanding now. You will need to do more finishing work after the parts are assembled so no need to go crazy yet. The exception would be the cross guard, since it is large with smaller details I would recommend doing a little more filling and sanding on that part. I wouldn't start doing any paint at this stage.
Use some form of epoxy to hold all of the pieces together. When you are ready to do the final attachment of a piece put a little bit of epoxy on the threaded rod where the piece will sit. Then thread the rod over the epoxy to help secure it. Put a decent amount of epoxy where the two printed parts will touch so that is squished together when the parts meet. Depending on the product used you can then wipe the epoxy away, trying to smooth it out over the lines where the parts meet. Don't be tempted to move or twist a part that you have set for final alignment, let it rest until cured.
I have used JBWeld with success, though there are a lot of other products that will work just as well or better. You could use something lighter like super glue, as the threaded rod will do most of the work holding it all together, however I like that I can use the epoxy to better fill cracks and sand down nicely at the end.
Note: Thread the cross guard and Blade part1 onto the rod together as if they were one piece, due to the way blade part1 fits onto the cross guard you can't twist them together after one piece is on the rod.
Finishing
After assembly you can start finishing work. Sand down any extra epoxy that comes up between the cracks where each part meets another part. Get your filler of choice and go to town! I personally like Bondo glazing and spot putty, using a nitrile glove you can spread a bit onto your finger and smoothly spread it across the parts. It starts drying quickly, but while it's wet it is really easy to smooth and shape. You could also add a little bit of acetone or other products to the putty to thin it out and almost "paint" the putty on. However, this can be harder to manage, won't be as thick, and you would be working with even more toxic chemicals, so be extra careful.
After putting down a filler and letting it dry, start sanding, then filling and sanding until you get it to a more manageable stage. Once it is really close to your desired smoothness levels you can start painting. I recommend starting with a filler primer, or at least a sandable primer, usually used for paining cars. Start by giving it a coat of primer, then sand it, then primer, then sand, same as the filler until you get it where you want. At this stage I am usually working with fairly high grits of sandpaper, like 200-2000, usually starting with a higher grit after each new coat. I also recommend wet sanding if at all possible, especially here, as the sandpaper will be super fine and the paint will come off easy, so the water helps the process a lot.
If you are unfamiliar with this process there are a lot of tutorials and things out there, but the basics are, apply some filler where you want the print to be smoother, then sand it down starting with a lower grit sandpaper and moving up higher and higher until you get it as smooth as you want. The lower the grit the more the sandpaper will remove. So if you are sanding raw plastic you will want something a lot lower to knock down the layer lines a bit. I'd recommend hitting the plastic quickly with a really low grit sandpaper to just knock down the really high layer lines, but don't worry about it being very smooth after that. When you start adding the fillers and sanding from there is when you will start to see the smoothness arrive, as the fillers will "fill" in the valleys of the layers. After the filler step move on to paining with a filler primer and doing the same, fill then sand steps, until you are happy with the smoothness.
Depending on what your final top coat paint is going to be it may show a lot of imperfections, or it might hide them more. You likely won't be sanding your final paint.
For the top coats of paint we personally used Black 4.0 (The worlds blackest paint) to give it a really really cool super matte finish that makes it reflect very very little light and really stands out. (Unless you're in a dark room) This is a really cool way to go, however, it is really expensive, and very hard to paint with. It is also extremely fragile, and you won't be able to put a clear coat over the top to protect it at all. It also comes off really easily if touched and will run onto the things it touches. If you plan to take it out and/or let others handle it this may not be the way to go if you want it to stay in good shape. A more traditional way would be using a few coats of regular black spray paint followed by a few coats of a protective clear coat. This will more more durable, while still looking really nice! I would still recommend going with as matte paint and clear coats that you can, in my opinion this fits the eternal black and soul sucking nature of Nightblood. However, you could go more glossy and I'm sure it would still look amazing! It all just depends on the look you are going for.
For the grip, we used some small nylon sewing thread tightly woven around each grip section with a small amount of clear glue under to hold it together and onto the printed parts. It ended up looking really nice, and feels really nice to hold. It was also really easy to do. You could go with a leather grip or something else as well.
Finally, make sure to put this thing in a sheath and don't listen to the voice. It may want to destroy evil, but I don't think it really knows what that means..
Download the Base 3D file for free and read our breakdown of how we prepped, printed, and post processed the file to achieve the end result; or, you can skip the first bit of prep work and download the prepped 3D files if you plan to follow the same post processing steps as us and want a head start.